Strip and Wire forming in India
YSM
Established in 1979 – YSM today has evolved into the Top 3 global leaders in providing Stamping and Bending manufacturing solutions. Our greatest asset is not just an effective workforce, but our well-trained and competent support team of over.
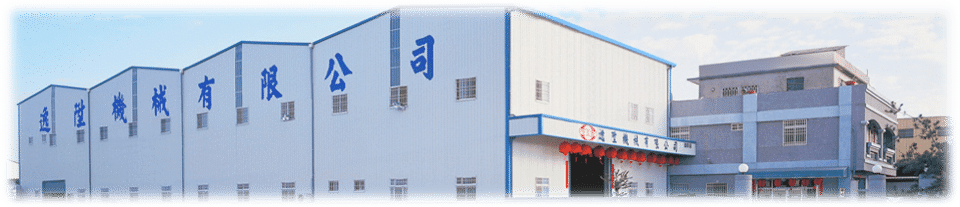
Strip and Wire forming
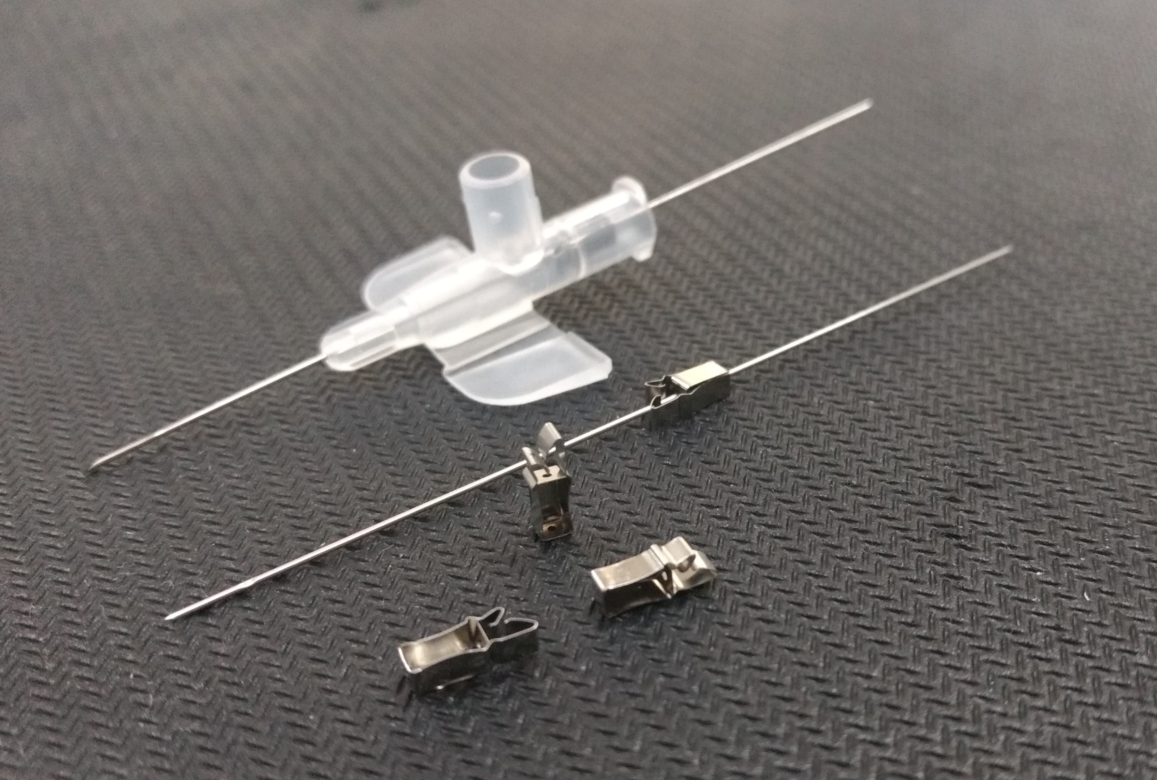
Materials Used in Strip and Wire Forming:
The choice of materials is fundamental in strip and wire forming, as it affects the final product’s properties and performance. Common materials used include:
- Steel: Various types of steel, including stainless steel and carbon steel, are frequently employed due to their durability, strength, and corrosion resistance.
- Aluminum: Aluminum offers a lightweight option with good corrosion resistance, making it suitable for numerous applications.
- Copper: Copper’s excellent electrical conductivity makes it ideal for electrical components and connectors.
- Brass: Brass, an alloy of copper and zinc, is valued for its combination of corrosion resistance and aesthetic appeal.
2. Techniques in Strip and Wire Forming:
Strip and wire forming encompasses several techniques, each tailored to specific applications and requirements:
- Bending: Bending is the most basic technique, involving the deformation of a metal strip or wire to create angles, curves, or complex shapes. Bending machinery, such as press brakes, are often used for precision bending.
- Roll Forming: Roll forming involves feeding a metal strip through a series of rollers that gradually shape it into a desired profile. This method is commonly used for producing long, continuous pieces with consistent cross-sections, such as structural components.
- Stamping: Stamping uses a die and press to cut or form metal strips into specific shapes. This technique is ideal for mass production of small, intricate parts like washers or gaskets.
- Wire Coiling: Wire coiling machines wind metal wire into coils of various shapes and sizes. This process is vital for manufacturing springs, which find applications in countless devices and mechanisms.
- Wire Drawing: Wire drawing reduces the diameter of a wire by pulling it through progressively smaller dies, resulting in a smoother surface finish and precise dimensions. This is commonly used in the production of electrical wires and cables.
3. Applications of Strip and Wire Forming:
The versatility of strip and wire forming has led to its widespread use across multiple industries:
- Automotive: Strip and wire formed components are found throughout vehicles, including seatbelt springs, exhaust hangers, and fuel injector clips.
- Electronics: Precision electrical connectors, terminals, and wiring harnesses are often created using strip and wire forming techniques.
- Aerospace: The aerospace industry relies on these processes for manufacturing aircraft components such as brackets, clamps, and sensor housings.
- Medical Devices: Springs and clips used in medical devices, as well as components for surgical instruments, are produced through strip and wire forming.
- Construction: Building and construction applications include the production of curtain wall clips, ceiling hangers, and earthquake bracing components.
- Consumer Goods: Strip and wire forming is integral to the production of everyday items like paperclips, zippers, and furniture brackets.
- Renewable Energy: Components for solar panel installations and wind turbines, such as clips and brackets, are manufactured using these techniques.
4. Significance in Modern Manufacturing:
Strip and wire forming plays a crucial role in modern manufacturing for several reasons:
- Customization: These techniques allow for the production of highly customized components to meet specific design requirements.
- Cost-Effectiveness: Mass production capabilities of strip and wire forming processes make them cost-effective for producing large quantities of components.
- Precision and Consistency: Advanced machinery and automation ensure precise and consistent product dimensions, minimizing defects and waste.
- Versatility: The ability to work with a variety of metals and alloys makes strip and wire forming adaptable to diverse industries and applications.
- Efficiency: High-speed production and minimal material waste contribute to efficient manufacturing processes.
5. Future Trends in Strip and Wire Forming:
As manufacturing technologies continue to evolve, strip and wire forming is poised for further innovation:
- Advanced Materials: The development of new materials with enhanced properties, such as shape memory alloys, may open up new possibilities in strip and wire forming applications.
- Automation and Robotics: Increasing integration of automation and robotics in strip and wire forming processes will further improve efficiency and reduce labor costs.
- Digitalization: The adoption of digital design and simulation tools will enhance precision and reduce prototyping time.
- Sustainability: Continued efforts to reduce material waste and energy consumption will align strip and wire forming with sustainable manufacturing practices.
In conclusion, strip and wire forming is a versatile and indispensable manufacturing process with a wide range of applications across industries. Its ability to transform flat metal strips and wires into intricate components has significantly impacted modern manufacturing, offering customization, cost-effectiveness, precision, and efficiency. As technology continues to advance, strip and wire forming is likely to remain a key player in shaping the future of manufacturing.